本ページはプロモーションが含まれています
工場内での安全性を確保するために、指さし確認は欠かせない手法です。目で確認し、指をさして声に出して確認することで、ヒューマンエラーを防ぎ、事故を未然に防止することができます。しかし、実際の現場では指さし確認が徹底されていないことも少なくありません。本記事では、指さし確認の重要性、従業員が指さし確認を怠った場合の指導方法について詳しく解説します。
指さし確認とは?
指さし確認とは、確認するポイントを指で指しながら声に出して確認する作業手法です。この一連の動作により、注意力が高まり、作業ミスを防ぐ効果があります。日本の多くの工場や建設現場で採用されているこの手法は、安全管理の基本として位置づけられています。
指さし確認の目的
- ヒューマンエラーの防止
見落としや勘違いを防ぎ、正確な確認作業を行う。 - 安全性の向上
作業者がリスクを認識し、安全を確保するための意識を高める。 - 作業の標準化
誰が作業しても同じ手順で確認が行われ、一定の安全基準を維持する。
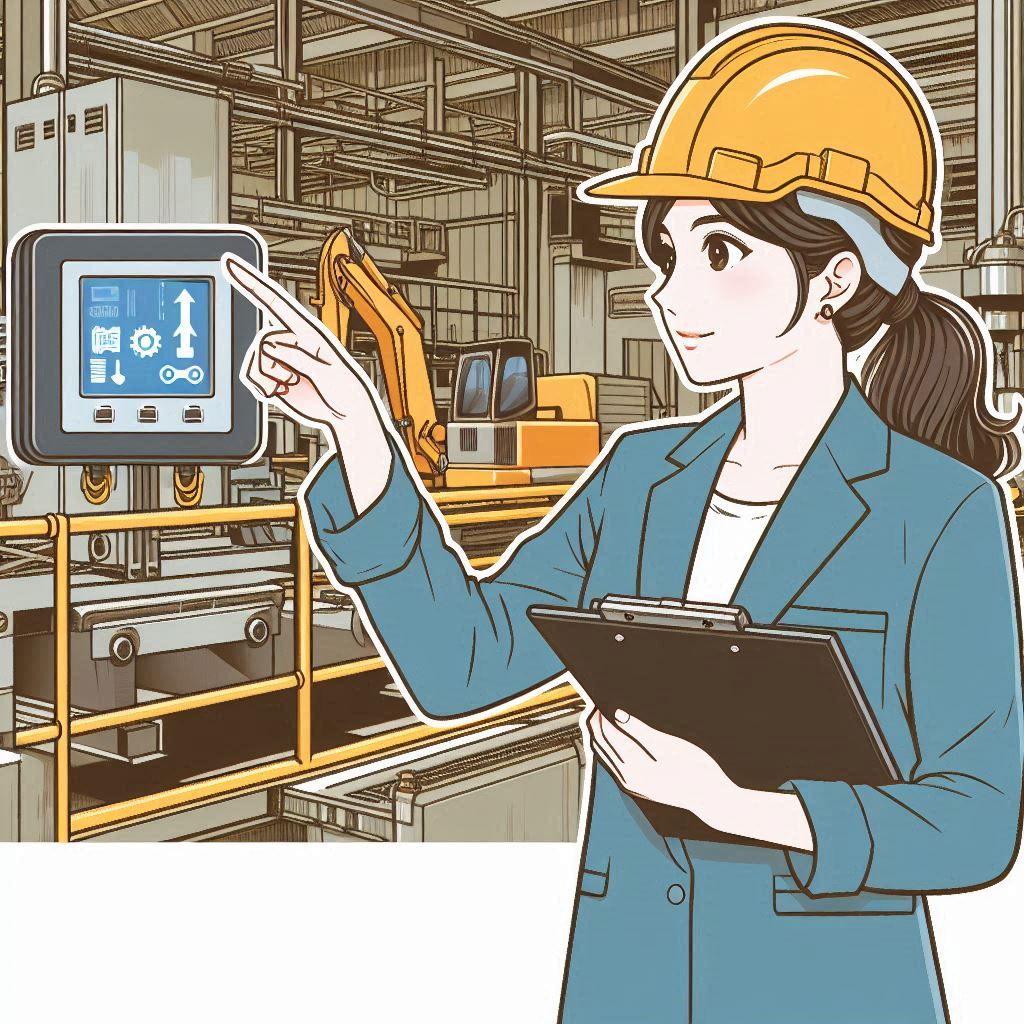
通路での指さし確認
工場内には、多くの通路や交差点があり、これらの場所は事故が発生しやすいポイントです。特に、フォークリフトや重機が通行する場合、交差点での確認不足が重大な事故につながるリスクがあります。そこで、交差点での指さし確認が非常に重要です。
交差点での指さし確認の手順
- 交差点に近づく前に減速する
通路の交差点に近づく際には、必ず減速し、周囲の状況を確認する準備をします。 - 確認ポイントを指さし、声に出して確認
交差点の左右と前方を指さしながら、「左よし、右よし、前よし」と声に出して確認します。これにより、見落としを防ぎます。 - 他の作業者や車両の存在を確認
周囲に他の作業者や車両がいないかを目視で確認し、安全が確認できたら通行を開始します。 - 交差点を慎重に通行
確認後は、交差点をゆっくりと通行し、いつでも停止できるように注意を払います。
交差点での指さし確認の効果
- 衝突事故の防止
視界が悪い交差点でも、指さし確認によって他の作業者や車両との衝突を防ぐことができます。 - 作業者間のコミュニケーション向上
指さし確認により、作業者同士のコミュニケーションが強化され、安全な作業環境を維持できます。 - リスクの早期発見
指さし確認を通じて、潜在的なリスクを早期に発見し、適切な対策を講じることが可能です。
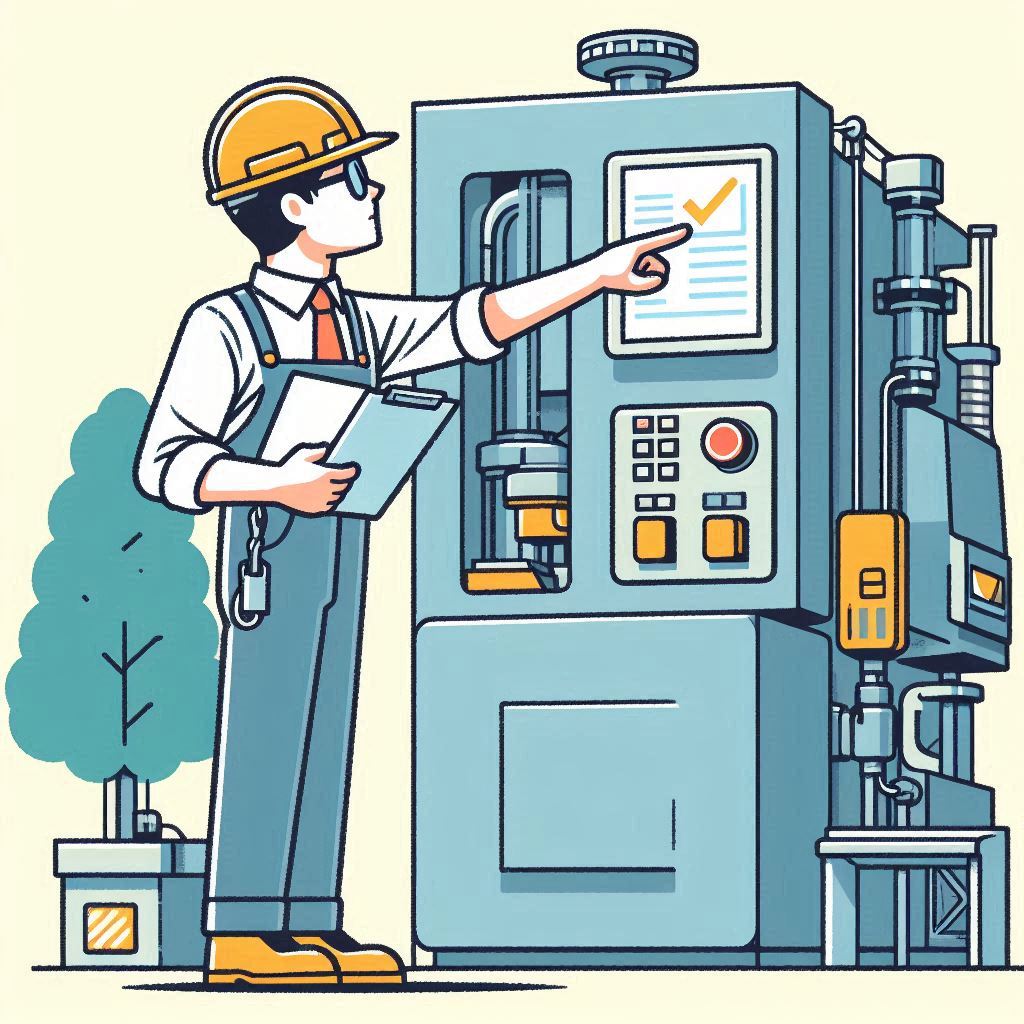
ホイストやクレーンでの指さし確認
ホイストやクレーンの操作は、重量物を取り扱うため、特に高い安全意識が求められます。玉掛作業では、吊り荷の安定や周囲の安全確認が不可欠です。指さし確認は、これらの作業においても重要な役割を果たします。
玉掛作業における指さし確認の手順
- 吊り荷の安定確認
吊り荷が安定していることを確認し、「吊り荷よし」と声に出して指さし確認を行います。荷が不安定な場合、作業を中止し、再度玉掛を行う必要があります。 - 作業エリアの安全確認
吊り荷を移動させる前に、作業エリア内に人や障害物がないかを確認します。特に吊り荷の移動経路を指さしながら「経路よし」と確認し、万全を期します。 - ホイストやクレーンの状態確認
操作前にホイストやクレーンのブレーキやワイヤーの状態を指さし確認し、「機器よし」と声に出して確認します。異常があれば、操作を中止して整備が必要です。 - 操作の開始
全ての確認が完了した後、操作を開始します。操作中も指さし確認を継続し、吊り荷の動きや周囲の状況に注意を払います。
玉掛作業における指さし確認の効果
- 吊り荷の落下防止
吊り荷の安定を確認することで、荷の落下やバランスの崩れを防ぎます。 - 作業エリアの安全確保
作業エリア内の安全確認により、他の作業者や設備への接触事故を防止します。 - 機器の不具合による事故防止
ホイストやクレーンの状態確認を通じて、機器の不具合による事故を未然に防ぎます。
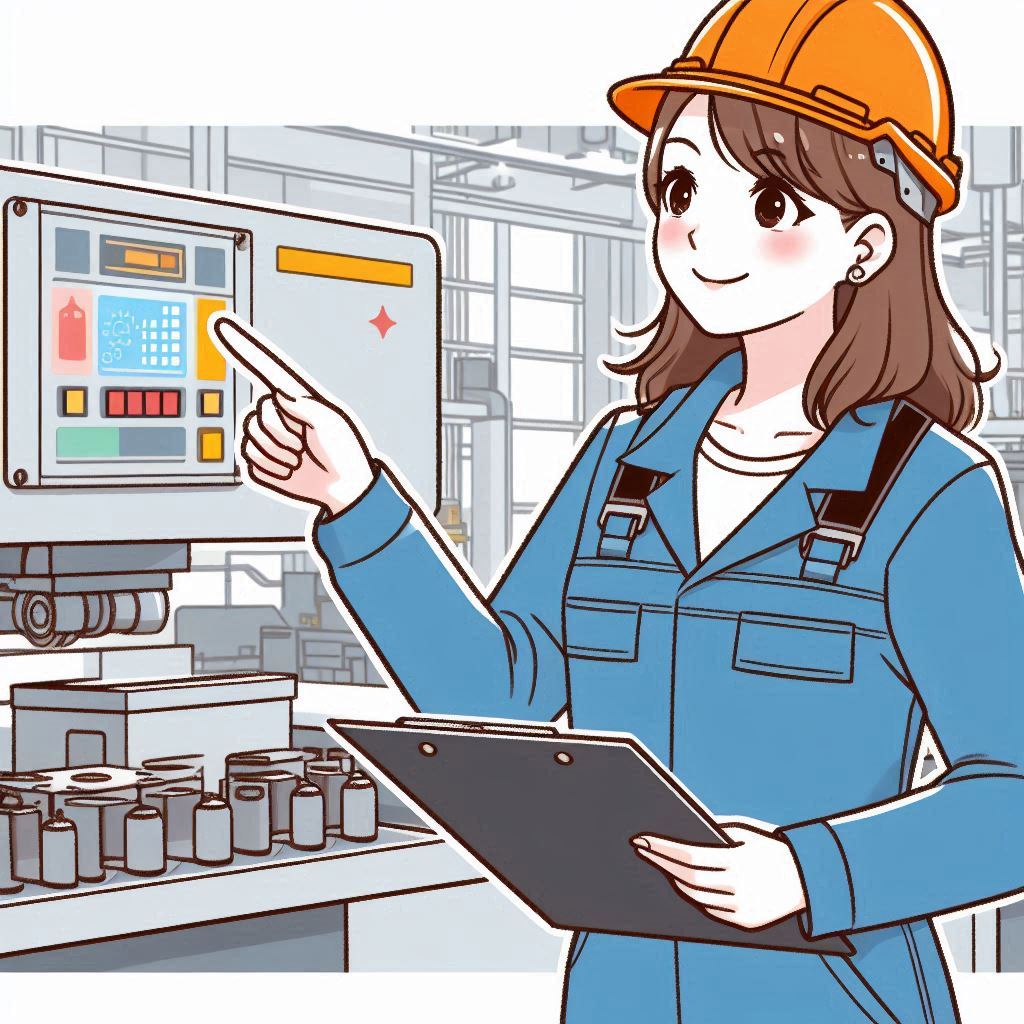
指さし確認の指導方法
工場内での指さし確認は重要ですが、従業員がこれを怠ることもあります。そのような場合には、適切な指導を行い、指さし確認の徹底を図る必要があります。
原因の特定と理解
まず、従業員が指さし確認を行わない理由を把握します。時間的プレッシャーや指さし確認の重要性の認識不足など、さまざまな要因が考えられます。原因を理解することで、適切な指導が可能になります。
重要性の再認識
従業員に対して、指さし確認が単なる形式的なものではなく、安全性を確保するための重要な手段であることを説明します。具体的な事例を挙げ、指さし確認を怠った場合のリスクを強調します。
実践的な指導と訓練
指さし確認を怠る従業員には、実際の作業現場で指さし確認の手順を教え、その場で実践させます。定期的な訓練を行い、指さし確認を習慣化させることが重要です。
改善指導とフォローアップ
指さし確認を繰り返し怠る場合には、個別に改善指導を行います。ただし、単に注意するだけでなく、改善策を一緒に考え、従業員が積極的に取り組むようにサポートします。フォローアップも行い、改善状況を定期的に確認します。
チーム全体での取り組み
指さし確認の徹底は、チーム全体で取り組むべき課題です。リーダーや管理者が率先して指さし確認を行い、チーム全体でその重要性を共有することで、従業員一人ひとりの意識を高めます。
まとめ
工場内での指さし確認は、事故防止と安全性向上に不可欠な手法です。交差点での確認やホイスト、クレーンの玉掛作業における確認手順を徹底し、従業員が常に指さし確認を行う習慣を身につけることが重要です。指さし確認を徹底することで、安全で効率的な作業環境を実現し、ヒューマンエラーのリスクを最小限に抑えることができます。
当ブログのトップページはこちらです
アラフィフ生産技術の日常
ブックマークして頂けると嬉しいです
よろしくお願いいたします
コメント