本ページはプロモーションが含まれています
製造業において、顧客からのクレーム対応や不具合発生時の対処は非常に重要です。顧客満足度を保ちつつ、問題の根本原因を特定し、再発防止策を講じることが求められます。本記事では、顧客からのクレームに対する対応方法や、内部での不具合発生可能性の調査手法、そして作業手順が守られなかった場合の適切な対処について、詳しく解説します。
不具合発生時の顧客対応: 基本ステップ
初動対応
顧客から不具合の報告を受けた際には、迅速かつ誠実な対応が求められます。以下の手順を踏むことで、顧客の信頼をたもちつつ、問題解決に向けた一歩を踏み出すことができます。
- ヒアリング: 顧客からのクレーム内容を詳細に聞き取り、問題の全体像を把握します。具体的な症状、発生時の状況、使用環境など、可能な限り詳しい情報を収集します。
- 初期分析: 顧客から提供された情報をもとに、内部での初期分析を行い、問題の範囲や影響を評価します。この段階での分析は、後続の調査や対応策の基盤となるため、慎重に行います。
- 一次対応: 顧客に対して、現在の状況や今後の対応計画を説明し、安心感を提供します。可能であれば、一時的な対策や代替品の提供など、顧客への配慮を示します。
根本原因の調査と対応策の提案
初動対応の後は、問題の根本原因を特定し、適切な対応策を提案するフェーズに移行します。以下のステップを参考にして対応を進めましょう。
- 詳細調査: 内部の専門チームを動員し、問題の詳細な調査を開始します。製品やサービスの製造・提供プロセス全体を見直し、特にリスクが高いと考えられる箇所に注目します。
- 原因の特定: 調査結果をもとに、問題の根本原因を特定します。原因が自社にある場合は、速やかに是正措置を講じおこないます。
- 報告と提案: 調査結果を顧客に報告し、再発防止策や補償案を提案します。この際、顧客が納得できるよう、事実に基づく証拠やデータを提示します。
顧客との信頼関係の維持
問題解決に至る過程で、顧客との信頼関係を維持することが最も重要です。以下のポイントを意識して対応を進めましょう。
- 透明性の確保: 調査の進捗や対応策について、定期的に顧客に報告し、透明性を保ちます。顧客が不安に感じないよう、常に状況を共有することが大切です。
- 柔軟な対応: 顧客の要望や状況に応じて、柔軟な対応を心掛けます。時には妥協が必要な場合もありますが、顧客満足度を最優先に考え、最善の解決策を模索します。
- 長期的な関係構築: 問題解決後も、定期的なフォローアップを行い、顧客との長期的な関係を維持します。信頼関係を強化するために、顧客のニーズや要望に応える姿勢を示しましょう。
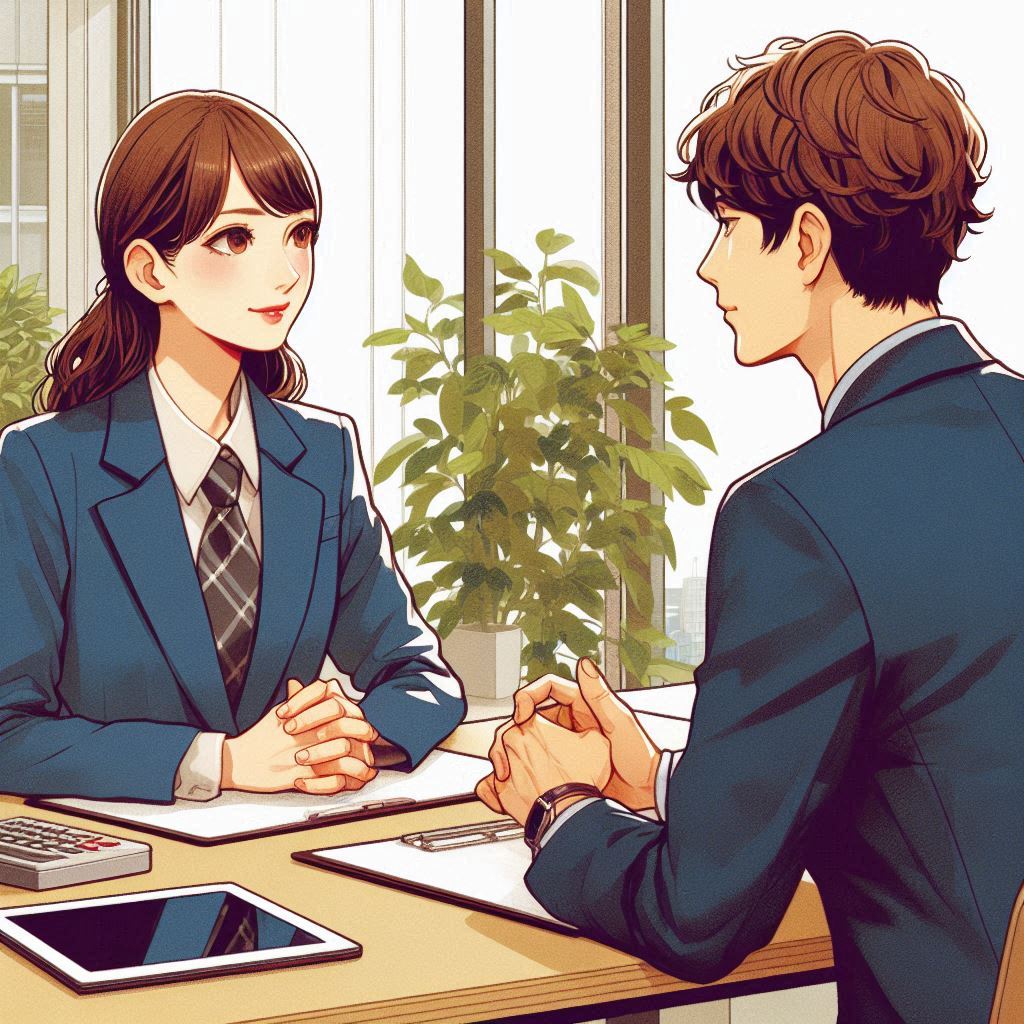
顧客側に原因がある?
時には、自社の調査結果から、問題の原因が顧客側にあると考えられる場合があります。しかし、顧客がそれを認めない場合には、慎重な対応が必要です。以下に、そのような状況での具体的な対処方法を解説します。
証拠の提供
顧客側に原因があると考えられる場合、まずは冷静にその証拠を集め、事実に基づくデータや記録を提示します。
- 客観的なデータ: 不具合の発生状況や使用条件に関するデータを集め、顧客に理解しやすい形で提示します。特に、同様の製品やサービスにおける業界標準や過去の事例と照らし合わせたデータが有効です。
- 比較分析: 顧客の使用条件と他の標準的な条件を比較し、問題の原因が顧客側にあることを示す分析結果を提供します。
専門家/第三者の意見を活用
顧客が自社の主張に納得してくれない場合、専門家や第三者機関の意見を求めることも効果的です。
- 第三者の意見: 信頼性の高い第三者の見解を得ることで、客観的な視点からの分析が可能になります。これにより、顧客も受け入れやすくなります。
- 専門家のサポート: 業界の専門家に依頼し、調査や分析を行ってもらうことで、より信頼性のある結果を提供できます。
穏やかなコミュニケーションと解決策の提案
顧客とのコミュニケーションは、常に穏やかで建設的なものにすることが重要です。
- 対話重視: 顧客が原因を認めない場合でも、対立せず、問題解決に向けた建設的な対話を心掛けましょう。
- 解決策の提案: 例えば、費用や作業を分担する形での対策や、試験的な処置を提案することで、顧客との折り合いをつけることができます。
顧客関係の維持を優先
最終的には、顧客との長期的な関係を維持することが最も重要です。
- 妥協と譲歩: 時には妥協や譲歩が必要になるかもしれませんが、顧客の満足度を高めつつ、自社の信頼性を損なわないような解決策を模索します。
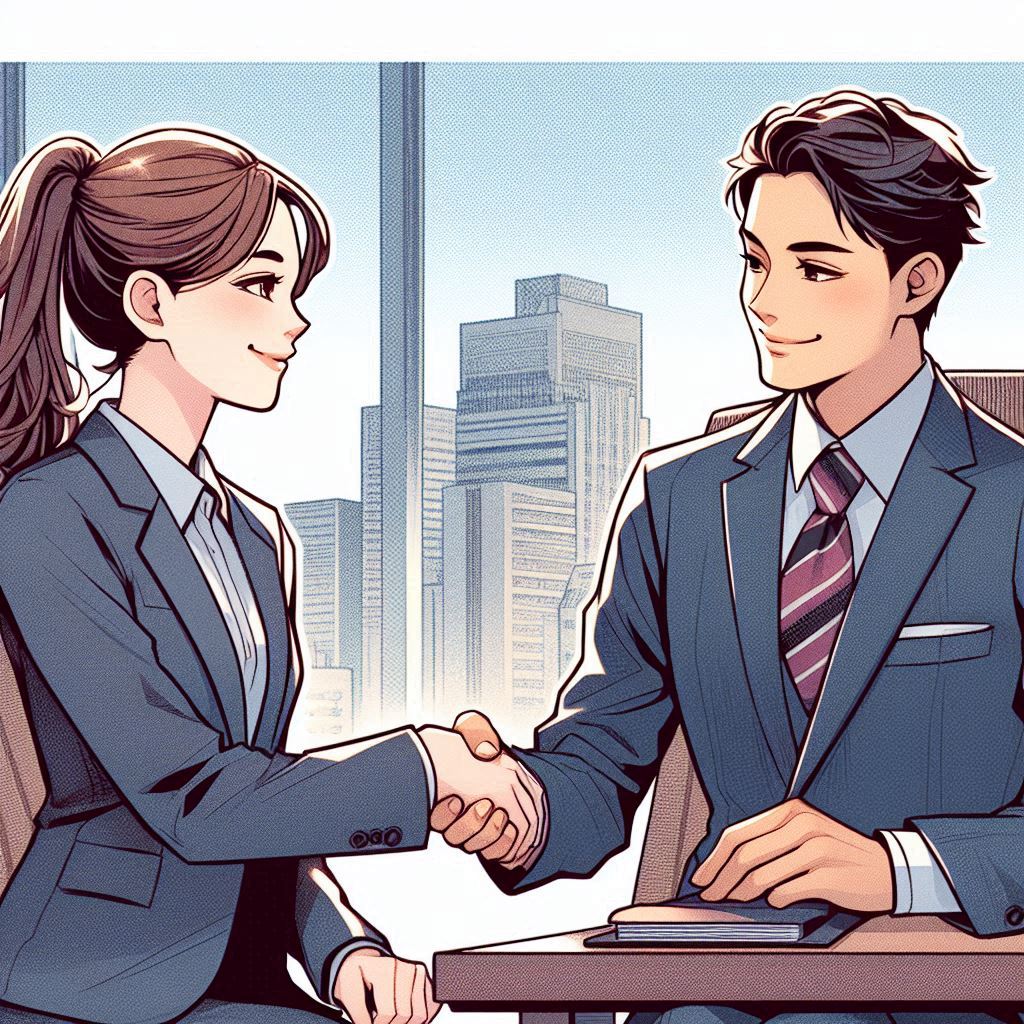
原因調査で注目すべきポイント
不具合の発生を未然に防ぐためには、発生可能性を徹底的に調査することが重要です。以下に、調査時に注目すべきポイントを詳しく解説します。
プロセスの各段階を詳細に分析
製品やサービスが提供されるまでのプロセス全体を通じて、不具合が発生する可能性がある箇所を特定します。
- 設計から最終使用まで: 設計、製造、検査、輸送、設置、そして最終的な使用環境に至るまで、各段階でのリスク要因を洗い出します。
- リスク評価: 各段階でのリスク評価を行い、どの部分で問題が発生しやすいかを特定します。
設備や治工具の状態
使用している設備や治工具の状態も重要な要素です。
- メンテナンス状況: 定期的なメンテナンスが適切に行われているか、設備の老朽化や治工具の精度がどの程度維持されているかを確認します。
- 設定とキャリブレーション: 設備の設定やキャリブレーションが適切に行われているかどうかも確認し、問題の発生源を探ります。
原材料や部品の品質
使用される原材料や部品の品質も、不具合発生に影響を与える要因です。
- 品質検査の実施: 原材料や部品が所定の品質基準を満たしているかどうか、定期的に検査を行います。
- サプライヤーの信頼性: 部品や原材料を供給するサプライヤーの信頼性を評価し、問題が発生するリスクを低減します。
- 保管状況:原材料や部品の使用前の保管状況にも注意しましょう。高温多湿を嫌う材料などあります。
作業環境と作業手順
作業環境や作業手順が、不具合発生のリスクにどのように影響しているかを評価します。
- 作業環境の適正化: 作業環境が適切であるかどうか、温湿度や照明などの環境要因が作業に与える影響を確認します。
- 手順の遵守状況: 作業手順が適切に守られているかどうか、現場での実際の作業状況を観察します。
作業者教育
作業者の教育の状況も、不具合の発生リスクに直結します。
- 教育プログラム: 作業者が手順や技術を理解しているかどうかを確認し、必要に応じて追加の教育プログラムを実施します。
- トレーニング: 実際の作業を通じたトレーニングが十分に行われているか、特に新入社員や異動者に対するOJT(オンザジョブトレーニング)が適切に実施されているかをチェックします。
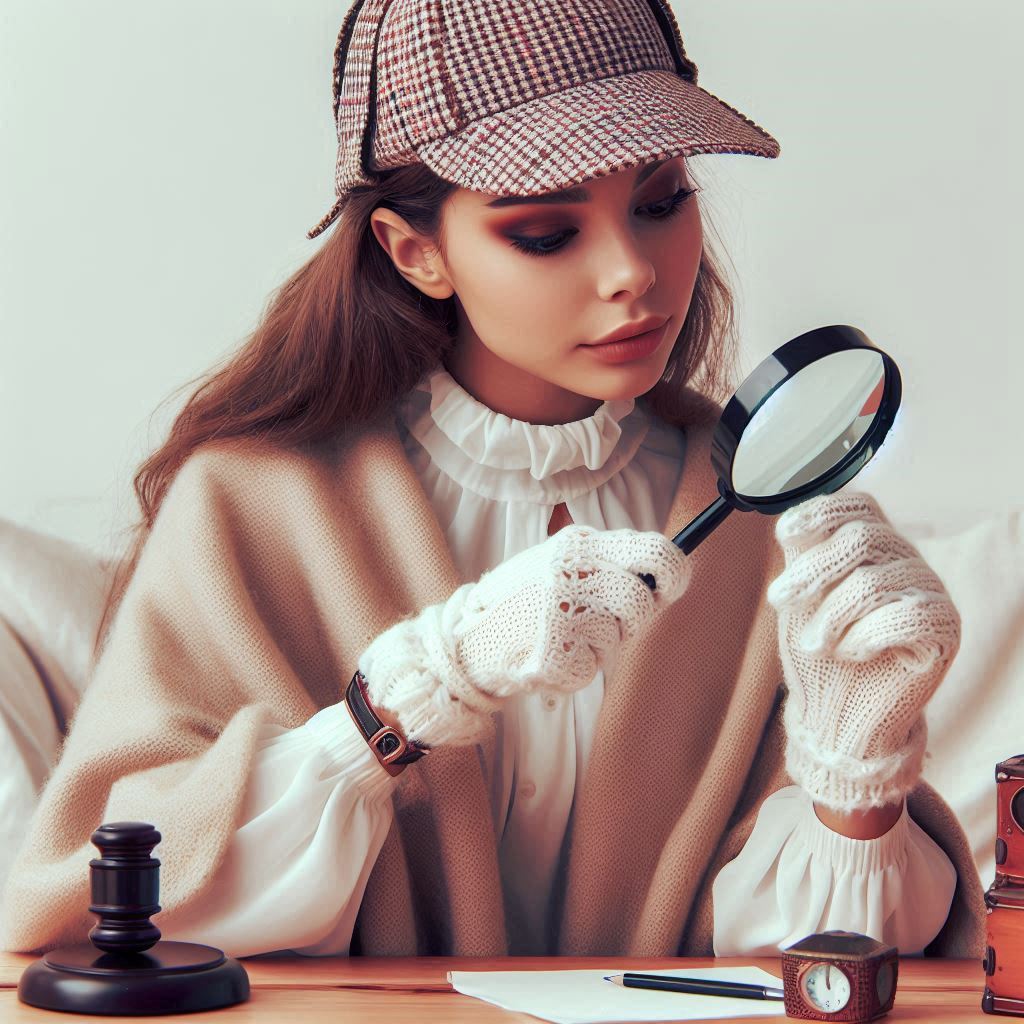
作業手順が守られていなかったら?
作業手順が守られなかった結果として不具合が発生した場合、その原因を特定し、再発防止策を講じることが重要です。ただし、作業者を責めるのではなく、なぜ手順が守られなかったのか、その背景を理解することが求められます。
作業者へのヒアリング
まずは、作業者に対して、なぜ作業手順が守られなかったのかを丁寧にヒアリングします。
- オープンな対話: 作業者が正直に話しやすい環境を整え、責めるのではなく、問題解決に向けた協力を求めます。
- 理由の特定: 手順が守られなかった理由として、「手順がやりにくい」、「サイクルタイム内に作業が完了できない」などがある場合、その根本的な原因を探ります。
手順と環境の再評価
手順や作業分担が現場の実態に合っていない場合や、実行が困難な場合は、手順の再評価が必要です。
- 手順の適正化: 手順が現実的であるかどうか、実行可能性を再評価し、必要に応じて手順の見直しを行います。
- 作業環境の改善: 手順が守られなかった背景に作業環境の問題がある場合は、その改善を検討します。例えば、設備や道具の改良、作業スペースの見直しなどが挙げられます。
教育の強化
手順の理解度や技能に問題がある場合、再教育をおこないます。
- 再教育: 手順が適切に理解されているか、再確認し、必要に応じて再教育を実施します。「なぜその作業が必要なのか」を理解してもらうことで、作業者に考える意識を持ってもらえます。
- OJTの実施: 実際の現場でのオンザジョブトレーニング(OJT)を通じて、作業者が手順を守りながら効率的に作業できるようサポートします。
継続的なモニタリングとフィードバック
改善された手順が現場で適切に守られているかを継続的にモニタリングします。
- モニタリング: 改善策が効果を上げているかどうか、定期的にチェックし、必要に応じてさらなる改善を行います。
- フィードバックの活用: 作業者からのフィードバックを積極的に取り入れ、手順や環境の改善に役立てます。
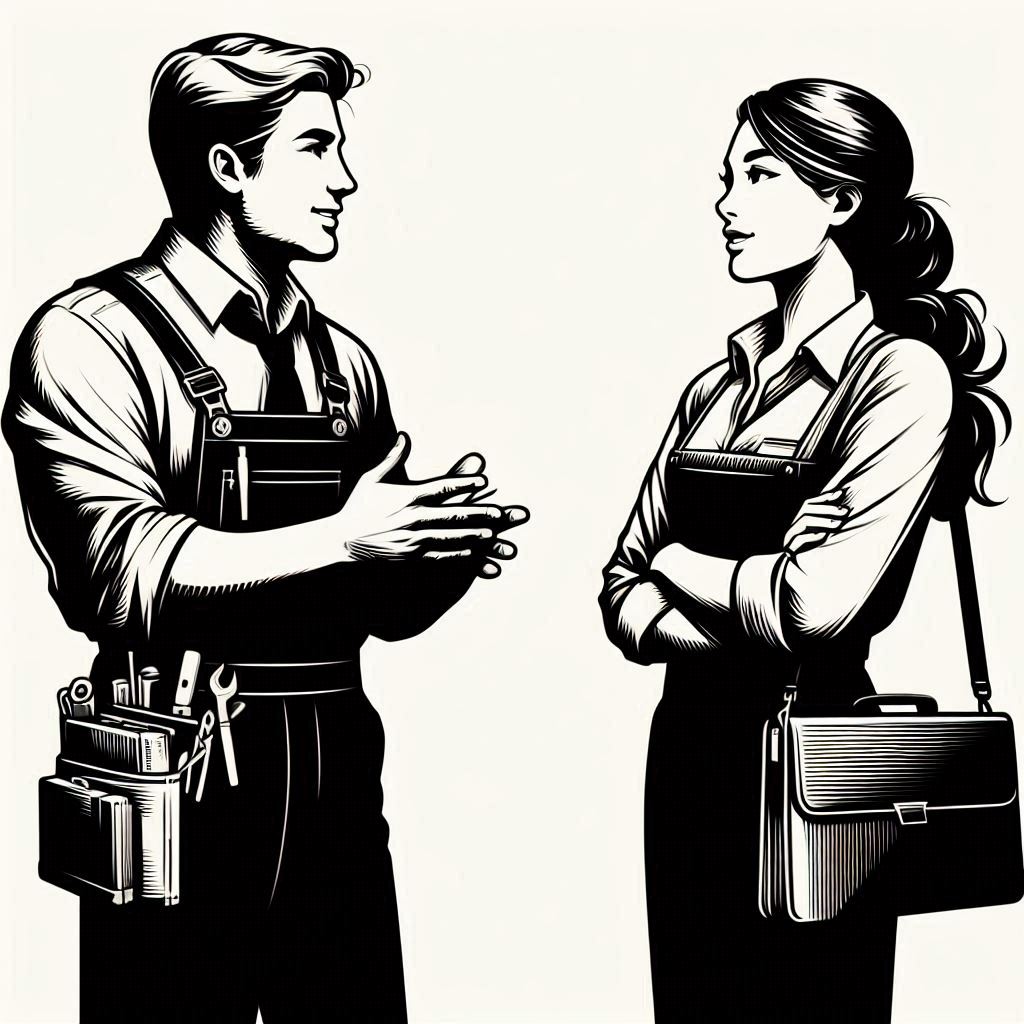
まとめ
不具合対応においては、顧客との信頼関係を維持しながら、問題の根本原因を特定し、適切な対応策を講じることが求められます。特に、顧客側に原因があると考えられる場合や、作業手順が守られなかった場合には、冷静で慎重な対応が必要です。継続的な改善を通じて、不具合の再発防止と品質向上を目指しましょう。
当ブログのトップページはこちらです
アラフィフ生産技術の日常
ブックマークして頂けると嬉しいです
よろしくお願いいたします
コメント