本ページはプロモーションが含まれています
製造工場では、データ分析の能力がますます求められています。効率の向上や問題の発見、品質の改善にはデータを正確に分析し、そこから得られた結果を活用することが重要です。この記事では、特別なツールを使用せずに現場で簡単に実践できるデータ分析能力の向上方法を紹介します。
基本的なデータ収集
最初のステップとして、データを正確に収集することが求められます。工場では、作業員が手動でデータを記録する場合もありますが、機械の稼働データや生産記録が自動的に収集されることもあります。重要なのは、以下の基本原則に基づいてデータを収集することです。
- 一貫性:同じ基準や形式でデータを記録し続けることが重要です。これにより、後でデータを比較したり、傾向を分析したりする際に信頼性が高まります。
- 正確性:入力ミスや誤差が生じないよう、データの記録方法を統一し、確認作業を行うことが推奨されます。例えば、同じ単位を使う、正確なタイムスタンプをつけるなどの手法です。また記録する作業者ごとに記録値が異なっていることはぜったい避ける必要があります。どこからどこまでの寸法や時間を記録するのかなどを明確にしておきましょう。
- リアルタイム性:可能な限りリアルタイムでデータを記録することで、状況の変化を迅速に把握でき、適切な対応が取りやすくなります。
EXCELを使って分析
複雑なデータ分析ツールを使わなくても、EXCELを活用してデータを分析することは可能です。例えば、工場で日々の生産数や不良品の割合を集計し、次のような簡単な指標を手計算で確認することができます。
- 平均値:全体のデータの傾向を把握するために有効です。例えば、1日の平均生産量を計算し、その基準と比較して増減を把握する。
- 割合や比率:不良品率や稼働時間の割合など、特定のデータ間の関係性を確認する際に活用します。例えば、総生産数に対しての不良品の割合を計算することで品質管理に役立ちます。
- トレンドの追跡:過去数日間や数週間にわたって、データの変化を追跡することで、改善傾向や問題点を発見できます。
現場の知識を活用
データ分析の結果を正しく解釈するためには、工場の現場の知識が不可欠です。例えば、生産工程や機械の特性を理解している作業員は、データに現れる変化の原因を察知しやすくなります。以下のポイントに注目すると、データの変化を深く理解し、適切な対応策を見つけやすくなります。
- 作業工程とデータの関連付け:特定の作業がデータにどう影響しているのかを確認し、それぞれの数値を業務内容と結びつけて考えることで、改善のポイントを発見できます。
- 問題発生時のヒストリー確認:過去に問題が発生した際のデータを見直し、そのときの状況と比較することで、再発防止策の手がかりを得ることができます。
グラフ化してみる
ヒストグラムや散布図など、簡単なグラフを作成することも効果的です。これにより、データの分布や傾向を視覚的に把握しやすくなり、重要なパターンが見つけやすくなります。
- ヒストグラム:データの分布を確認し、特定の範囲にデータが集中しているか、外れた値があるかを視覚的に確認できます。
- 散布図:2つの変数間の関係を調べる際に役立ちます。例えば、作業時間と不良品率の相関を確認することで、何らかのパターンが浮かび上がるかもしれません。
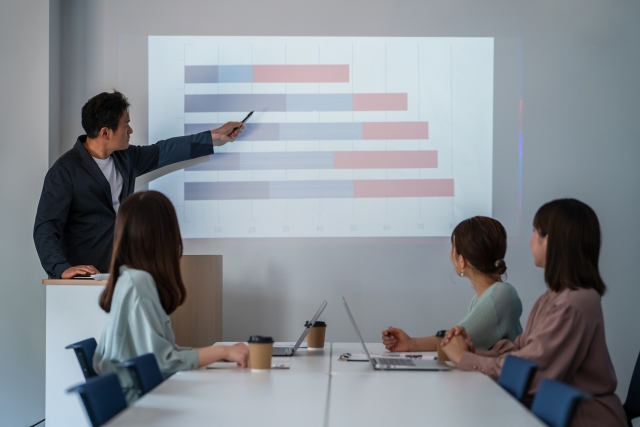
その理由をしらべる
データが変化したとき、その理由を正確に究明することは、工場の運営において極めて重要です。悪化したデータの原因を見つけることで、問題の再発を防止し、早急に対策を講じることができます。また、データが良くなった場合、その成功の要因を特定することで、さらなる改善や他の分野への応用が可能になります。
問題の早期発見
データが悪化した場合、迅速にその原因を特定することで、問題を早期に発見し対策を講じることができます。例えば、生産効率が低下している場合、機械の故障や作業者のミスが原因であるかもしれません。これらの問題を放置していると、さらなるコスト増加や生産の遅延が発生する可能性があります。原因を究明することで、的確な対応が取れるため、トラブルを未然に防ぐことができます。
またデータを調査する頻度も重要です。月初から問題が発生していたにも関わらず、データ分析が月末だけだったため、対応が遅れてしまったというのは避けたいですよね。
よくなった理由も大事
良くなったデータについても、その背景にある要因を特定することで、同じ成功を再現したり、他の工程にも応用したりすることができます。たとえば、特定の作業手順を改善した結果生産性が向上したのであれば、その手順を標準化し、他のチームでも同様の改善を行うことが可能です。これにより、全体的なパフォーマンスの向上が期待できます。
効果的なリソース配分
原因を究明することで、改善のために必要なリソースを効果的に配分できます。特定の問題が一部の工程に集中している場合、その工程に対してメンテナンスやトレーニングを強化することが適切です。また、良い結果が出た場合には、その成功を他の部門にも展開し、リソースを効率的に活用できます。
根本原因への対策
表面的なデータの変化に対応するだけでは、同じ問題が再発する可能性があります。データの悪化や改善の理由をしっかりと理解することで、根本的な原因を見つけ出し、再発防止策を講じることが可能になります。例えば、品質不良が増加した場合、その原因が一時的な問題であれば短期的な対策で済むかもしれませんが、根本的な原因が作業プロセスや機械の問題であれば、長期的な改善策を講じる必要があります。
PDCAサイクルの向上
悪化したデータや良くなったデータの原因を究明することは、PDCAサイクル(Plan, Do, Check, Act)の「Check」と「Act」に直接影響を与えます。対策を施した結果がどうだったかを正確に評価し、次の行動に反映させるためには、データの変動理由を理解することが欠かせません。これにより、改善活動の精度が向上し、持続的な改善が可能になります。
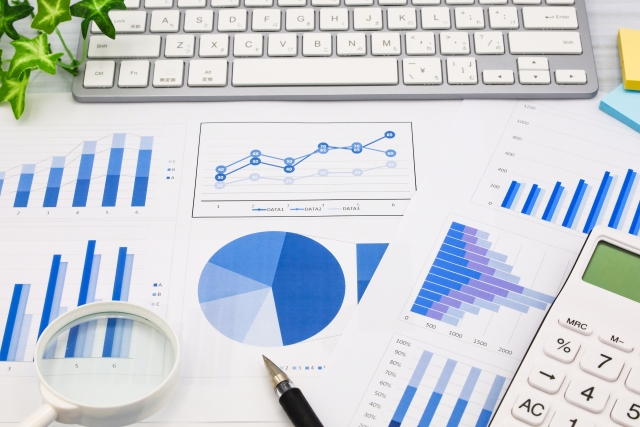
データ分析の着目点
データを収集した後、分析の焦点となる重要なポイントを見つけるためには、以下の方法を参考にすると効果的です。
目的を明確にする
データ分析の最初のステップは、何を知りたいのか、何を改善したいのかという目的を明確にすることです。目的が不明確だと、データのどこに着目すべきかがわかりにくくなります。例えば、品質の向上が目的ならば、不良品の発生率やその原因となる工程に焦点を当てるべきです。
異常値や外れ値に注目する
データの中には、他のデータから外れた値や異常に高い・低い値が含まれていることがあります。これらの異常値や外れ値は、何らかの問題や改善点を示している可能性があります。異常な値を検出したら、その原因を調べ、現場の状態と照らし合わせることで、根本的な問題を発見することができます。
トレンドを確認
データが時間軸に沿ってどのように変化しているか、トレンドを確認することも重要です。例えば、生産量が一定期間増加している場合、作業効率の向上が影響しているかもしれませんし、逆に減少している場合は機械の故障や作業の効率低下が原因かもしれません。トレンドを把握することで、パターンを見つけ出しやすくなります。
平均や中央値と比較
集めたデータの平均値や中央値を計算し、各データポイントがそれらとどう異なるかを確認します。平均よりも極端に高いデータや低いデータがあれば、その部分に注目して原因を探ることができます。例えば、通常よりも生産数が少ない日があれば、その日に何が起きたのかを調べると改善のヒントが見つかるかもしれません。
相関関係を探る
2つ以上のデータ間に相関関係があるかどうかを確認することも効果的です。例えば、不良品の発生率と特定の作業者の勤務日が一致している場合、その作業者のスキルや手順に問題があるかもしれません。このように、異なるデータセット間の関係を分析することで、原因と結果の関連性を明らかにできます。
フィルタリング
データを特定の条件でフィルタリングし、特定の状況やパターンを探ることも有効です。例えば、特定のシフトや機械でのみ不良品が多発している場合、その時間帯や機械に問題がある可能性があります。フィルタリングを使うことで、データの中に隠れている問題点を見つけやすくなります。
知識との結びつけ
データ分析は単なる数値の処理ではなく、現場の業務知識と結びつけて解釈することが重要です。現場での作業の流れや特定のイベントがデータにどう影響するかを考えながら分析を進めると、データの背後にある意味が理解しやすくなり、改善に役立つポイントが見つかりやすくなります。
グラフの活用
データの分布や相関を視覚的に確認するために、ヒストグラムや散布図を活用するのも効果的です。ヒストグラムを使えば、データがどの範囲に集中しているか、外れた値はどこにあるかが一目でわかります。散布図を使えば、2つの変数間の関係性を視覚化し、特定のパターンや相関を見つけやすくなります。
PDCAサイクルの評価
データをもとに改善活動を行った場合、PDCAサイクルを用いて、計画した対策が実際にどのように効果を発揮したかをデータで確認します。具体的には、計画前と後のデータを比較し、改善の成果を確認することが大切です。効果がない場合は、新たな着眼点を見つけるための手がかりになります。
まとめ
データ分析では、単にデータを集めるだけでなく、目的を明確にし、異常値やトレンド、相関関係などに注目することで重要なポイントを見つけることができます。データが示す内容を現場の知識と結びつけて解釈することで、具体的な改善につながる着眼点を発見することができます。データを記録するだけではもったいない。「これはなぜ?」という意識を持つことが重要ですね。
当ブログのトップページはこちらです
アラフィフ生産技術の日常
ブックマークして頂けると嬉しいです
よろしくお願いいたします
コメント