本ページはプロモーションが含まれています
工場改善提案を効果的に提出し、現場や上層部の理解と評価を得るためには、提案のメリットを具体的にアピールすることが重要です。この記事では、改善提案をより強力に説得力あるものにするためのポイントを詳しく解説します。
改善効果の数値化
提案のメリットを具体的な数値で示すことは、上層部や他部門に対して効果を理解してもらうための有効な方法です。例えば、改善により生産性が向上した場合、「生産効率が〇%向上することで、年間〇〇万円のコスト削減が見込まれる」といった具体的な数字があれば、提案内容に説得力が増します。
改善効果を数値化するための例:
- 稼働時間の短縮:1日の稼働時間が30分短縮できれば、その時間を年間ベースで計算し、得られるコスト削減効果を算出します。例えば、稼働時間が短縮されることで、電気代や人件費などの直接コストの削減につながります。
- 生産ロスの削減:改善によって作業効率が向上し、仕損品が減少する場合、年間の仕損品減少分をコスト換算して数値化します。例えば、年間1,000個の不良品が減少することで、材料コストや手直しコストの削減額を見積もります。
こうした数値は、上層部が改善提案のインパクトを容易に理解できるだけでなく、現場のモチベーション向上にもつながります。具体的な効果が見えると、現場の協力も得やすく、改善に対する賛同が得られやすくなります。
エネルギー削減による効果額
生産性向上により稼働時間が短縮された場合、電気代や冷却コストなどのエネルギーコストも削減できるため、これも提案に含めると効果的です。例えば、機械の稼働時間が減少することで消費電力が低下し、月間の電力コストが削減できるため、これを年間コストとして計算することで、改善提案の具体的な省エネルギー効果を示せます。
エネルギー削減効果のアピール方法:
- 電力消費の低減:稼働時間を1日あたり20分短縮できれば、その分の消費電力量を算出し、電力単価をかけ合わせて年間の電気代削減額を示します。特に、大型機械などは電力消費が大きいため、稼働時間短縮によるコスト削減は無視できません。
- 環境への貢献:エネルギー削減は環境保護にもつながり、企業の社会的責任(CSR)や持続可能な経営に貢献します。この点もアピールすることで、企業イメージ向上にもつながる可能性があると訴えることができます。
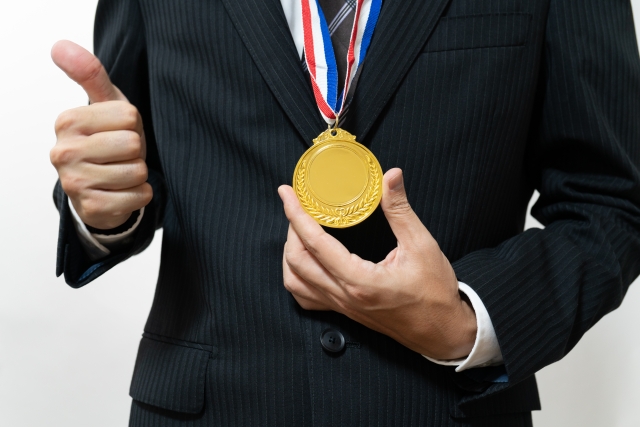
作業負荷軽減による品質改善効果
作業負荷を軽減することで、作業者の疲労が減少し、集中力が保たれるため、ミスによる不良品が減るという効果も期待できます。改善提案において、作業環境の改善が品質向上にもつながる点は非常に重要です。
具体的な改善例:
- 疲労軽減による品質不良の削減:疲労が減ることで作業者の集中力が向上し、注意力が高まるため、ヒューマンエラーによる不良発生率が低下します。たとえば、手動で行う工程での不良率が5%から3%に低下すれば、その分の不良削減コストを計算し、提案の中に含めます。
- 仕損品や手直し品の減少:ミスによって発生する仕損品や再加工品が減少するため、作業者の手間やコストも削減できます。これにより、現場全体の生産性向上が期待でき、コスト削減効果も発生します。
長期的なコスト削減効果
改善提案の多くは、短期的な成果だけでなく、長期的なコスト削減や品質向上が見込まれるものです。たとえば、エネルギー消費の削減やメンテナンス頻度の低減といった効果は、時間をかけて見えてくるものが多く、長期的な視点から評価することが求められます。
長期的な視点でのメリット:
- 設備の劣化防止:稼働時間の短縮やメンテナンスの頻度調整により、設備の摩耗や故障リスクが低下し、修理・交換コストが抑えられます。これにより、予算の節約とともに設備寿命の延長が期待されます。
- 改善の持続性:長期的に効果が続く改善は、企業全体の安定性や成長を支える要素にもなります。例えば、省エネルギー効果や不良率削減効果が長期間持続することで、企業全体のコスト削減が継続的に見込まれる点を強調します。
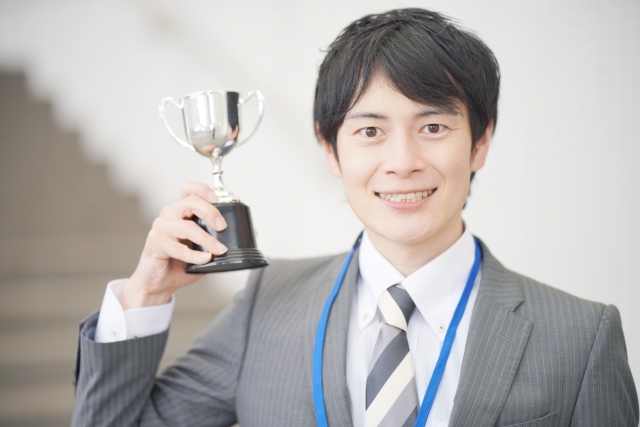
メンテナンスコスト低減
稼働時間が短縮されることで、設備のメンテナンスコストの低減が期待できます。ただし、このメリットを実現するためには、メンテナンスの頻度を従来の定期的なスケジュール(例:3か月に1回)から、定量的なスケジュール(例:1,000個生産ごと)に変更することが必要です。
メンテナンス頻度の調整によるコスト削減:
- 使用量に応じた保守:定量的なスケジュールにより、稼働頻度が少ない場合にはメンテナンス回数を減らすことができます。たとえば、製造数に基づいてメンテナンスを行うことで、必要以上の保守回数を避け、メンテナンスコストを最小限に抑えます。
- 無駄なメンテナンスの防止:定量的なスケジュールを採用することで、実際の稼働状況に合わせたメンテナンスが可能になり、設備の劣化を適切に抑えられます。これにより、過剰なメンテナンスコストを回避し、適正な運用管理が期待できます。
まとめ
生産性向上によるメリットは稼働時間低減での人件費のみを算出されることが多いです。紹介したとおり、エネルギー、メンテナンス、品質など改善活動で得られる効果は多岐にわたります。改善提案を提出するときにはそれらのメリットをアピールすることも忘れないでくださいね。あ、ウソはダメですよ(笑)
当ブログのトップページはこちらです
アラフィフ生産技術の日常
ブックマークして頂けると嬉しいです
よろしくお願いいたします
コメント