本ページはプロモーションが含まれています
製造業では改善提案を募集している工場おおいですね。
「年間〇件以上提出」などノルマにしている会社もあります。
「改善提案、めんどうくさいなぁ」と悩んでいる方に簡単にできるネタ集を紹介します。
改善提案の目の付け所
改善提案のネタを探すときの目の付け所。
・やりにくそう
・危ない作業
・無駄な歩行
・体の動き
などがポイントです。
ヒント、事例を紹介しますので、めんどうくさいと後ろ向きにならずに探してみましょう。
工具、治具の指定席化
工具、治具などの置き場を決める。
見落としがちですが大事なポイント。
「どこだっけ?」と引き出しを順番に開けて探す。
ほんの数秒でも無駄に違いない。
スポンジを工具の形に姿彫りにしてテプラで工具名を書く。
引き出しには中に入っているものを明示しましょう。
治具の固定
作業台の上で使うときに治具が動いてしまう。
これ、作業者が気づかない「やりにくい作業」です。
動かないように治具を固定するだけで作業性アップ。
固定するのがむずかしければ100円均一などでも売ってる「滑り止めシート」をひきましょう。
簡単でしょ(^^♪
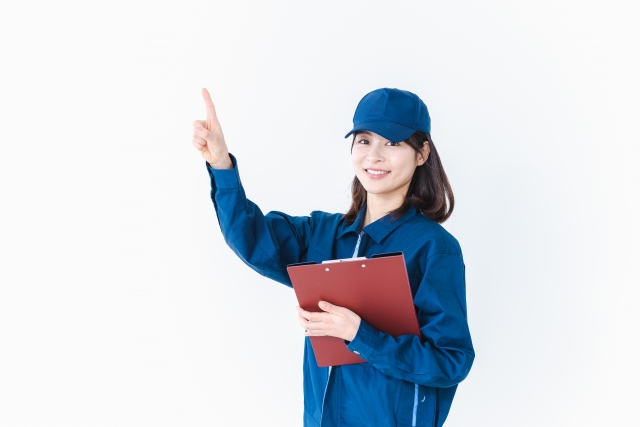
治具の多機能化
複数の治具を使うなら、ひとつの治具を多機能化がおすすめ。
治具や製品の持ち替え、セットのしなおしを削減できます。
1回の作業が1秒、2秒でも1日や1か月などの期間でみると大きいですね。
治具の軽量化
手で持って使う治具はもちろん、置いて使う治具でも重いのは作業者さん大変です。
段取り替えのたびに重い治工具を保管場所と作業台の間を運搬します。
材質の変更、肉抜きなどで軽量化しましょう。
重いものの取り扱いは腰痛などの原因にもなりますね。
作業範囲を見直し
特に大事なのが繰り返し作業での作業範囲。
作業者の人の動作がなるべく小さくなるように。
「遠くにあるものを手を伸ばして取る」って意外に重労働。
上は肩の高さ、下は腰の高さ。
正面を向いて立ったままで手の届く範囲に置くのがポイント。
場所が無くて振り向き作業になるときもなるべく近くにしましょう。
仕損の原因を対策
とくに喜ばれる改善は仕損対策です。
仕損は作った製品を捨てるのがもったいないだけでなく、もう1度作るのも無駄になります。
✔ 仕損になった原因はなにか?
✔ その原因を対策できないか?
を考えます。
「手扱いで設備にぶつけて変形させた」ならぶつける恐れがあるところにコーナースポンジをはる。
こんな簡単なことでも改善提案1件ですね。
設備のチョコ停を調査
設備がチョコチョコとまる、「チョコ停」ですね。
「いつものこと」で終わらせないで!
これも仕損対策と同じです。
✔ なぜ停まるのか
✔ その原因はなにか
を調査、対策しましょう。
設備を改造することで対策可能なら生産技術などに相談です。
「なんとかしてよ」という相談もしないよりはいいですが
「こうやれば対策できると思うんだ」の方が評価も上がりますね。
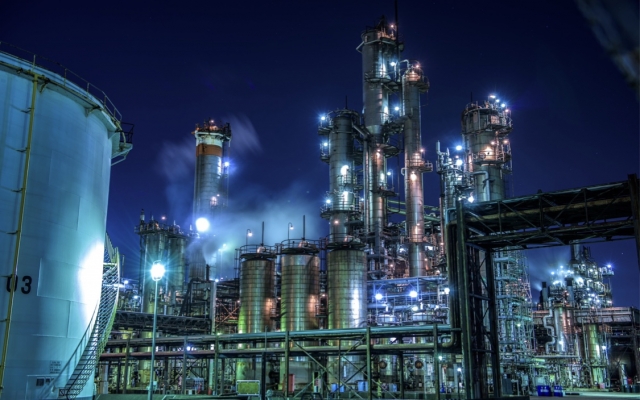
照明を変更
作業する時の照明は適切ですか?
手元が暗い、よく見えないなどは照明を設置しましょう。
照明は遠くから照らすより、なるべく近い方が明るさも増します。
高い位置に照明があるなら、それを近いところに移動。
これだけでもかなり良くなります。
また、明るければいいってものでもないです。
照明の色と製品の色が近いと「目が疲れる」の原因になります。
白い光よりも黄色の光の方が見やすいこともあります。
照明って奥が深いですよ。
エアガンを変更
エアガンってよく使いますね。
汚れや水滴を吹き飛ばすのに便利。
このときに使っている圧縮エア。
工場に設置されているコンプレッサーで作ったもの。
圧縮エアをつくるには電気代がかかります。
エアを吹き出す量を減らすのも大きな改善です。
パルスブローエアガン、インパクトエアガンなどがおすすめ。
普通のエアガンは吹きっぱなしですが、これはパルス状にエアを吹き出します。
エアの消費量が半分になるすぐれもの。
しかも止めて吹く、止めて吹くの繰り返しなので力をためて放出するため吹き飛ばす力がアップ。
省エネになって、パワーアップするなんて最高です(^^)/
設備の状態を見やすくしよう
始業前の設備点検をするために設備の裏側にまわってメーターを読む。
これも無駄な作業です。
メーターの位置を変更して作業位置で見えるようにしましょう。
裏側に回る無駄がなくなるだけでなく、作業者が設備の異常を早期発見してくれるかも。
「なんかおかしいけどまぁいいか」とならずに監督者に報告してくれますね。
可動部に安全カバーを
設備の可動部分や、高温になる部分に安全カバーを設置しましょう。
どこの工場でも「安全第一」ですね。
怪我して得する人は誰もいません。
固定の安全カバーをつけると段取り替えできない場合は開閉式のものをおすすめします。
ゴミ箱の容量を見直し
ゴミ箱がいっぱいになって何度もゴミ捨て場に行かないといけない。
これも無駄ですね。
ゴミ箱の容量を見直します。
1日の終わりに1度捨てに行くだけが目安。
さらにゴミの量を測定するものおすすめです。
ゴミってお金を払って捨てているんです。
ゴミの量を減らせばコストメリットも出ますね。
消耗品の無駄を減らす
消耗品の使用量を減らすのもおすすめです。
使用量が作業者まかせになっているものないですか?
溶剤を使うときにボトルからウェスにかけてました。
これをマニキュア落としのボトルに変更。
ウェスをもってボトルをプッシュするだけになりました。
作業も早くなり、使用量も減少、最高です♪
まとめ
かんたんにできる改善提案を紹介しました。
改善ポイントの見つけ方は冒頭で述べた通り。
・やりにくそう
・危ない作業
・無駄な歩行
・体の動き
など。
「もっと簡単な作業にできないかな?」を常に考えましょう。
自分の工程だけでなく、他の工程を見るのも参考になります。
ほかにもいろいろ書いてます
↓ 下記からご覧ください
サイトマップ
ブックマークして頂けると嬉しいです
よろしくお願いいたします
コメント