本ページはプロモーションが含まれています
工場の生産性を高めるための議論では、よく「部分最適」と「全体最適」という言葉が登場します。これらは生産性向上の手法として、それぞれに異なる目的と役割を持っています。しかし一方で、「部分最適はダメで、全体最適こそが目指すべきもの」という偏った意見が存在することも事実です。
この記事では、部分最適と全体最適の違い、それぞれのメリット・デメリット、両者を組み合わせる重要性について詳しく解説し、生産性向上を実現するための具体的なステップを提案します。
部分最適と全体最適の違い
部分最適とは
部分最適とは、工場の中で特定の部門や工程にフォーカスして改善を行う手法です。この改善は限定的な範囲で行われるため、短期間で効果が出やすい特徴があります。部分最適は具体的かつ実行可能な改善を通じて、現場レベルでの効率向上を目指します。
例
✔ 製造ラインの動線を見直して作業者の歩行時間を削減する
✔ 不良品検査工程のスピードを向上させるために新しい検査装置を導入する
メリット
✔ 改善効果がすぐに実感でき、モチベーションを向上させる
✔ 問題が明確なため、改善策が具体的で実行しやすい
✔ 小規模で開始できるため、改善に必要なコストや時間を抑えられる
デメリット
✔ 他の部門や工程との連携を考慮しない場合、全体に悪影響を及ぼす可能性がある
✔ 工場全体としての効率向上にはつながらない場合がある
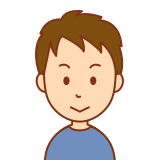
特定の工程が突出してしまった場合は、
人員数を減らして対応できる場合もありますね
省人となり効果が大きいですよ♪
全体最適とは
全体最適とは、工場全体のバランスを重視し、全体のプロセスを俯瞰的に捉えたうえで改善を行う手法です。工場内の部門間や工程間の連携を調整し、ボトルネックを解消して生産性を向上させることを目的とします。
例
✔ 各部門の生産計画を統合して、全体の効率を最大化する
✔ 作業を別工程や余裕のある作業者に振り分けるなどで無駄を削減する
メリット
✔ 工場全体のパフォーマンス向上が期待できる
✔ 無駄やボトルネックを効果的に解消できる
デメリット
✔ 改善の規模が大きくなるため、実現までに時間がかかる
✔ 抽象的な計画になりがちで、現場での実行が難しい場合がある
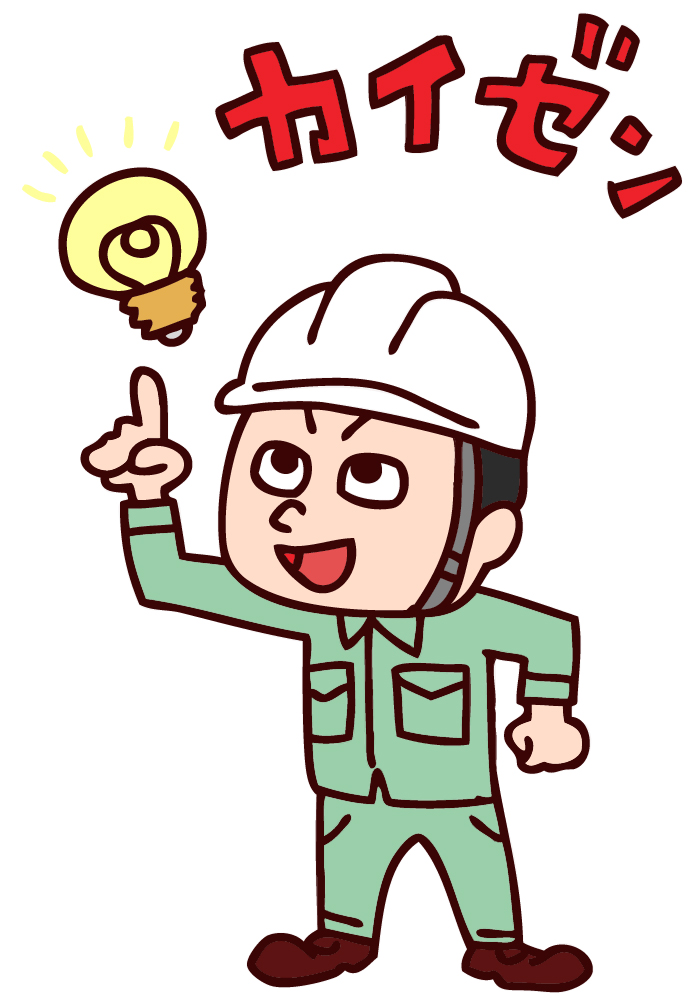
部分最適と全体最適の組み合わせ
「部分最適はダメで、全体最適だけを目指すべき」という意見は、一見すると正しいように思えます。全体の効率が高まることは重要ですが、実際の工場運営では、全体最適だけでは改善が進まないケースが多いです。
部分最適だけのリスク
部分最適だけに取り組むと、以下のような問題が生じる可能性があります:
- 局所的な改善が他工程での負担を増加させる
例: 製造ラインの速度を上げた結果、出荷工程が追いつかず在庫が溢れる。 - 全体のバランスが崩れる
一部の工程だけが効率化されても、他の工程との連携が取れなければ、全体としての改善にならない。
全体最適だけのリスク
一方で、全体最適だけを追求すると以下のような課題が生まれます:
- 現場での具体的な行動が曖昧になる
全体最適の計画が大規模で抽象的すぎると、現場の作業者が何をすべきかわからなくなる。 - 改善に時間がかかりすぎる
成果が見えるまでに時間がかかり、従業員のモチベーションが低下する可能性がある。
部分最適の積み重ねが全体最適につながる
部分最適と全体最適は、対立するものではなく、むしろ相互補完的な関係にあります。部分最適を積み重ね、その成果を全体最適の視点で統合することで、以下のような相乗効果を得ることができます。
- 現場改善が全体目標達成の基盤となる
部分的な改善活動で得られる知見やデータは、全体最適の計画立案に活用できます。 - ボトムアップ型の改善が可能になる
部分最適を重ねることで、現場からの積極的な提案やアイデアが出やすくなり、全体最適にも好影響を与えます。 - 小さな成功がモチベーションを高める
部分的な成功体験が従業員の自信とやる気を育み、全体改善への取り組みを活性化させます。
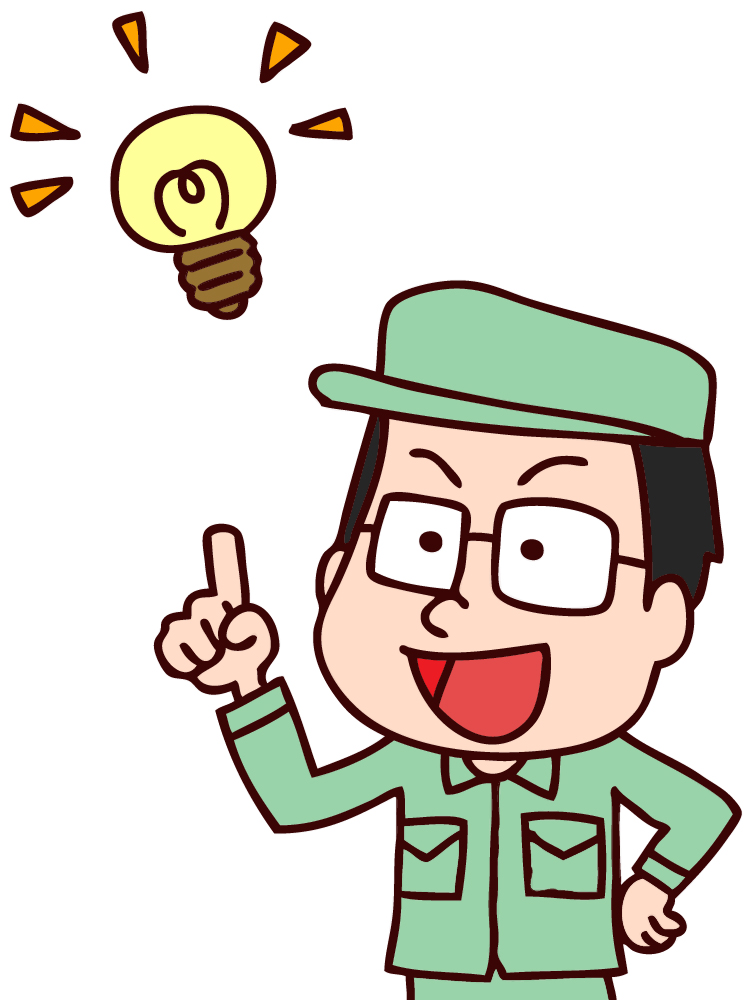
改善活動の実践ステップ
1. 全体目標を明確に設定する
工場全体として何を達成すべきか、明確な目標を設定します。この目標を現場の作業者にも共有し、部分最適の改善活動が全体目標にどのように貢献するのかを理解させます。
2. 改善活動の影響を全体で評価する
部分最適の改善結果が、他の部門や全体の効率にどのような影響を与えるかをデータで検証します。これにより、部分最適が全体のバランスを崩すリスクを最小化できます。
3. 小規模改善を積み重ねる
部分最適は小規模で開始できるため、早い段階で改善の成果を実感できます。この積み重ねが、全体最適の成功を支える基盤となります。
4. 全体最適と部分最適をつなぐ
改善プロジェクトのリーダーやマネージャーは、部分最適の成果を全体目標に統合する役割を果たします。全体最適の視点を持ちながらも、現場の声を聞き、具体的な改善をサポートします。
5. 部分最適の成功事例を全体に展開する
成功した部分的な改善の事例を他部門や他工程に展開し、工場全体の生産性向上につなげます。
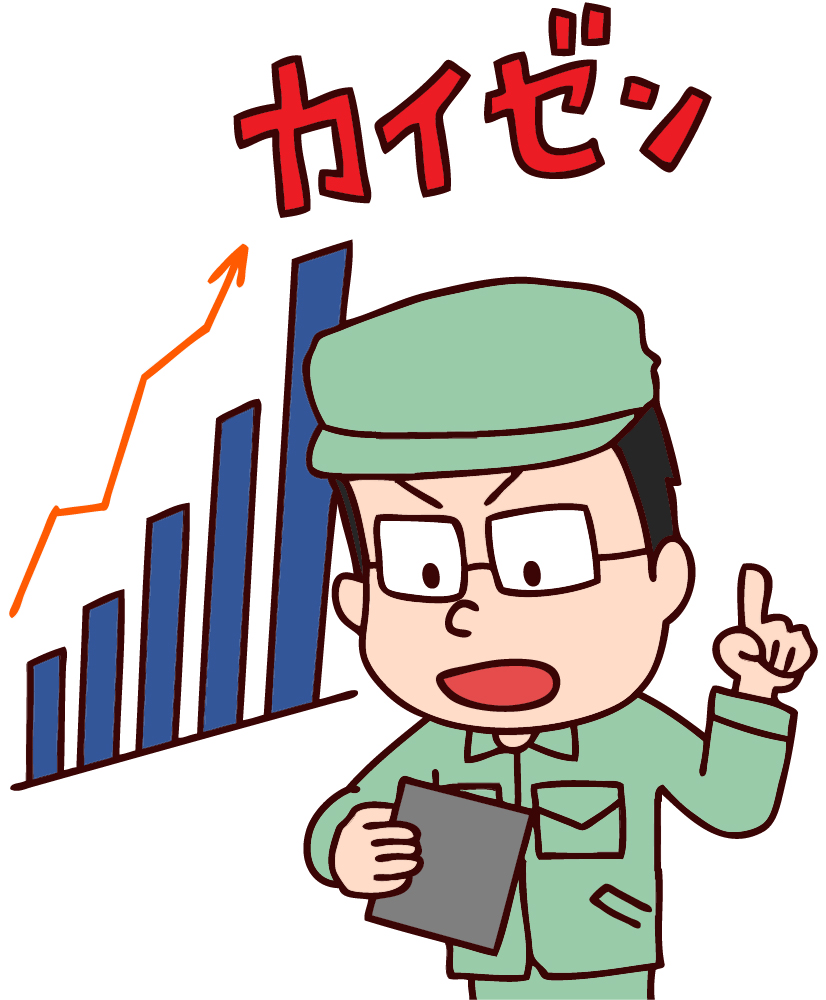
具体的な事例:部分最適と全体最適の統合
ケーススタディ:製造ラインの改善
- 部分最適:
2名で分担して行っている作業を改善して作業負荷を軽減する - 全体最適:
部分最適で軽減した負荷を1名で行えるようにする
1名で全ての作業をこなせない場合、次工程の負荷が少ない作業者に振り分ける
まとめ
「部分最適」と「全体最適」は、生産性向上においてどちらも欠かせない要素です。一方だけに偏るのではなく、両者をバランスよく組み合わせることで、短期的な成果と長期的な効果を同時に得ることができます。
当ブログのトップページはこちらです
アラフィフ生産技術の日常
ブックマークして頂けると嬉しいです
よろしくお願いいたします
コメント